Flight Design MC: Full Metal Concept
A born trainer, this spacious, docile workhorse flies like Wichita tin
![]()
|
You want to fly the MC?," asks Flight Design's amiable national sales manager, John Gilmore. I'm at the company tent during Sebring, Fla.'s U.S. Sport Aviation Expo, and the MC is on my must-fly list.
"Sure, when?"
"Right now!" exclaims John.
"Now?"
It's late in the day. I'm tired. I haven't flown in a week or so. And I haven't flown at Sebring in a year.
A glance to the cloudy, hazy west reveals a low, low sun: We've got 45 minutes---tops---until LSA-legal sundown. I had hoped to have more time. Still, few people have flown the MC. And the aircraft will be swamped once the show starts.
"Let's do it," I say, and we head for the hangar. Soon, I'm shaking hands with Tim-Peter Voss---no less than the chief engineer of flight and ground test for Flight Design Germany.
The door sill is low to the ground: Climb-in's a breeze. The comfortable interior feels familiar, as it should: It's like the CTLS in which I got my sport pilot ticket.
"I haff not flown at the Sebrink," Voss says in his crisp German accent, "and have no American license, zo you muss do everysink, the radio, the airspess, yes?"
Hmm. So now I get to demonstrate my ineptitude with the unfamiliar Sebring airspace, as well as fly a new airplane next to its test pilot?
Well, life is meant to be an adventure. If we must fail, fail grandly!
![]() The MC is Flight Design's first metal airplane. It's built in the Ukraine and assembled in Germany before delivery to the United States. |
We fire up the Rotax 912 ULS.
"Okay, Tim," I say as we taxi. "Do you have any suggestions?"
"No, whateffer you vant to do," he replies. His arms are crossed as though he has no intention of even touching the controls.
Roger that. Ground handling with the steerable nosewheel and brake hand lever on the console is a breeze, just like the CTLS.
But right off, I notice the MC feels...solid, like a bigger airplane.
Tower clears takeoff, I power up, and off we go.
Climbing out, I immediately feel like I'm piloting a much heavier airplane. Not unlike---dare I say it---a Cessna 150 or 172.
This isn't to say that the aircraft's control forces are "trucky." In fact, they're about average, well harmonized and plenty responsive.
No, what I'm sensing is the inherent aerodynamic stability and balance of the airplane. It feels, well, like an old, familiar friend.
You can't beat the cabin, either. At almost 52 inches, you could call it downright cavernous. Believe me, four feet, four inches of shoulder room feels positively roomy.
The solid handling feel stays with me as we climb out over the lake to the west, eyeballs scanning for traffic, to do a little air work.
Stalls are nominal, straight ahead and come with plenty of warning burble. Break and pitch down are slight, well-forewarned and instantly recovered from by relaxing stick and/or feeding in a touch of power.
Hanging on the prop at mid-40s indicated is a no-brainer. And aileron effectiveness in slow flight is excellent. It's designed that way to provide roll control even below stall speed---a great feature in a training airplane, which is the prime market Flight Design envisions for the MC.
Pulling back sharply on the stick in level flight, then letting go---testing for dynamic stability, a trick Rans Aircraft's top dog, Randy Schlitter, taught me---yields reassuring results.
![]() The MC's spacious cabin comfortably seats pilot and copilot, and can be outfitted with optional Dynon EFIS avionics. |
The MC pitches up, I let go of the stick, and it pitches below the horizon, speeds up, then pitches above the horizon to start the sequence all over again.
That oscillation is called a phugoid. Angle of attack stays near-constant, but pitch varies because the airspeed and altitude are constantly interchanging until balance is regained.
Dynamically stable airplanes---i.e., those that return to straight-and-level flight automatically---are ideal for training purposes.
The MC's phugoids damp out after a couple gentle upsy-downsies---very nice indeed.
After the hurried air work (the murky conditions get grayer once old Sol lands on the horizon), I still wonder why the MC feels bigger and heavier. Its basic empty weight is just 795 pounds, which is in the same ballpark as other LSA.
For comparison, here are some other LSA empty weights:
⢠Cessna Skycatcher: 830 pounds
⢠Flight Design CTLS: 770 pounds
⢠PiperSport: 740 pounds
That leaves the MC 375 pounds or so of payload after full fuel, about 30 more than the Skycatcher.
I look over at my test-pilot passenger, and ask, "Anything you want to show me, Tim?"
"No, vhateffer you like," Voss says, content to let me do my worst. At least he's not scared---yet. But then, he's a test pilot.
I crank some turns. Rudder is effective, but you don't need much, unlike the CTLS, which is more of a rudder airplane in climbs, turns and landings. I catch myself overstomping the rudder a bit, and lighten up.
Darkness descending: time to land.
It has been a mere 25 minutes since takeoff, yet I feel so completely comfortable and---here's the key word---competent in the MC that I don't even ask Voss for landing pointers.
I toggle in partial flaps with the electric switch, idle the throttle, set up a 500 fpm descent and ride that pony down to a smooth landing as if I've flown the MC for many hours.
![]() |
What a confidence builder! Flight Design has clearly optimized the MC's training chops: This is one forgiving, comfortable airplane.
The gear absorbs what little bump I give it without bouncing us back up, like a spring steel main might. Again, a lovely trainer's attribute.
That shock-absorbing quality, which absorbs 50% of landing loads, comes from the laminated composite construction of the main-gear legs. As John Gilmore tells me later, not only does the wide six-foot, six-inch stance make for docile, solid touchdowns and tracking, but the many layers of carbon-fiber laminates minimize spring-back.
"The idea," Gilmore explains, "is to have the layers ’slide' on each other when overloaded, rather than break. It's like the skin of a banana, which will split if you bend it too far. It's very strong, but it's designed to fail before loads transfer to the airframe. And you can swap out the gear in 45 minutes."
MC stands for Metal Concept. The airplane is primarily aluminum skin over the welded-steel-tube fuselage and
aluminum-ribbed wing. The rounded, bluntish nose section is the only major composite airframe part.
In a flight-school environment, metal airplanes are easier, more familiar and cheaper for traditional repair shops to deal with. Metal airplanes also can endure unsheltered ramp parking better than composites, which fare better in a hangared environment.
Later in the week, I sit down with Flight Design's CEO, Matthias Betsch, for a chat about the airplane.
"It has a different character than the CT line," he starts off. "The CT is more sporty, speedy and responsive. So far, everyone who has flown the MC agrees with you: It feels much heavier than it is. That's what we wanted. It's the perfect airplane for schools: very forgiving, easy to land, easy to fly and more stable in turbulence."
He also touts the MC for older pilots used to stable Wichita tin. "They don't have to worry so much about converting to something different."
Betsch grins, "Of course, we have targeted it for flight schools, but if you learn in one and like it, why not purchase one?"
Speaking to cruise performance, the MC gives away a bit to the fastest LSA out there: It's spec'd at 115 knots at max power, straight and level, and will deliver a 500 nm range at 97 knots.
![]() Tom Peghiny (left), Flight Design USA's president and founder, and John Gilmore, Flight Design's national sales manager, with the MC at U.S. Sport Aviation Expo. |
"Yes, we wanted something a little more stable," he continues, "but it also had to be fun to fly. We didn't want a big ’truck.'"
The MC is Flight Design's first metal airplane. Although Betsch's headquarters are in Germany, the aircraft (to date, 1,500 worldwide) are built in the Ukraine, then assembled, fine-tuned, fitted with avionics and test-flown in Germany before delivery.
I wondered if building a metal airplane was a challenge for veteran composite makers.
"We brought all that composite technology to the Ukraine, where our aircraft are manufactured," explains Betsch. "We set up the factory and trained all the people. But when we decided to build the MC, it was, in fact, easier. The Ukraine is known as a metal-airplane region. So it wasn't a big deal for them."
Betsch describes hiring veteran metal monkey Dennis Franklin, a mainstay at Sebring's Lockwood Aviation and a wizard working with lightweight aluminum structures. Indeed, he ran his own thriving company, Maxair, and made Drifter ultralights for years.
"Dennis helped us set up tooling in the Ukraine and refine the construction process. Ukrainian builders were used to working with aluminum sheet thicknesses suitable for big Antonov military airplanes, not for lightweight microlight and LSA airframes.
"In the end, Dennis had many good ideas and helped us build an airplane that's light but strong."
There's plenty more to share about the MC, but I'm running short on space.
Let me finish with a few summary adjectives: roomy, well-appointed interior; easy to fly; docile; fun; solid workhorse; beautifully finished; affordable at $98,993 (analog panel, 80 hp 912UL) or $113,823 (Dynon EFIS, BRS parachute system).
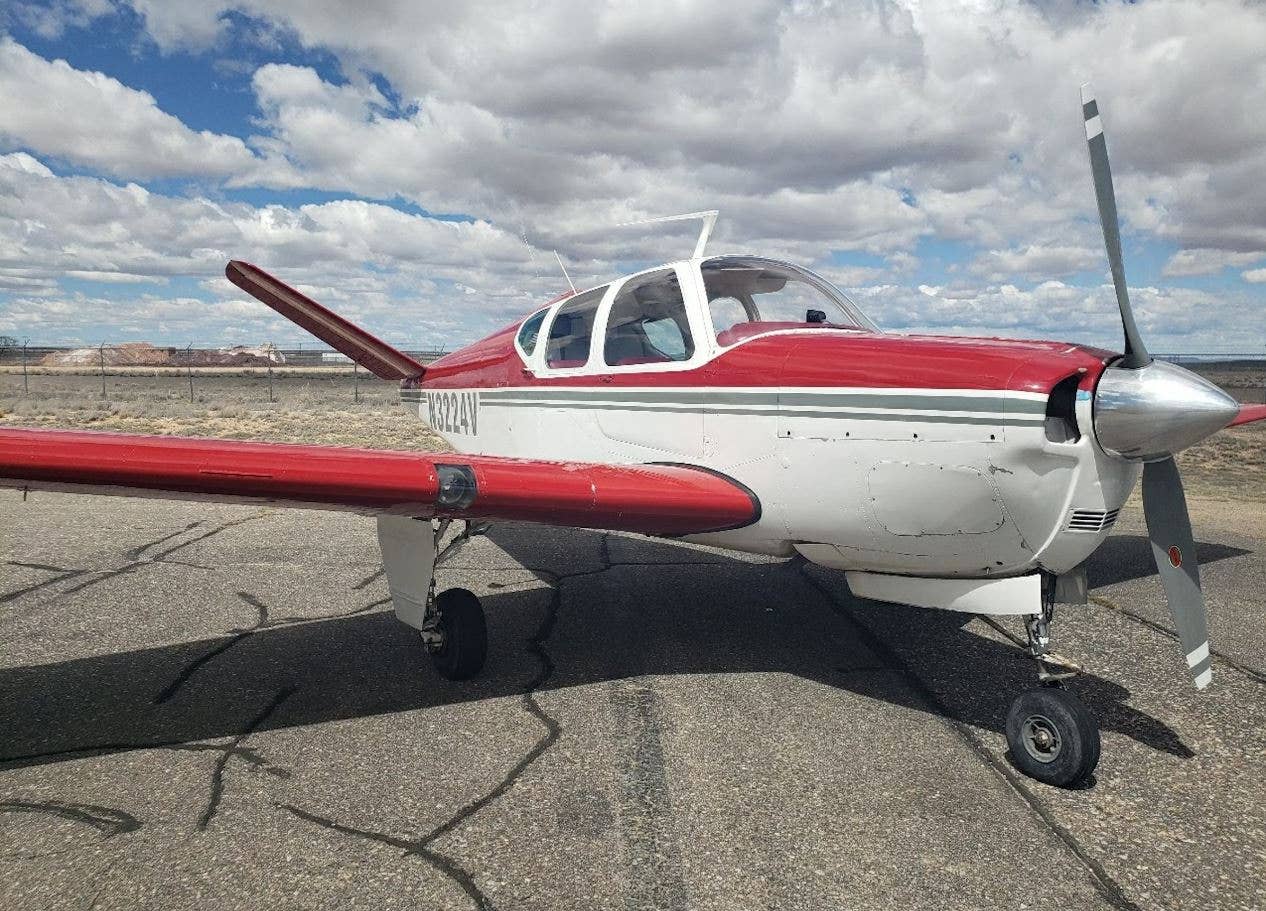
Subscribe to Our Newsletter
Get the latest Plane & Pilot Magazine stories delivered directly to your inbox